Smart Foundation for a Small Addition
Framing the floor inside a crawlspace foundation keeps a gable-end addition close to grade.
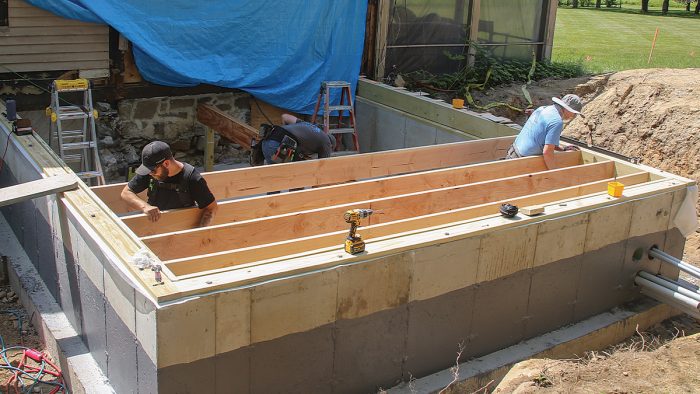
This 1780s Connecticut farmhouse needed a kitchen upgrade to replace a small, dated addition that clashed with the home’s aesthetic. To maintain a level floor and minimize disruption to the surrounding grade and a nearby tree, the builders chose a crawlspace foundation with the floor system framed inside it.
This approach preserved accessibility, protected the existing stone foundation, and facilitated future utility upgrades. Careful excavation, reinforced concrete footings and walls, and a thoughtfully framed floor system provided a solid base for the new kitchen and mudroom. The completed addition blends seamlessly with the historical home while offering modern functionality and design.
Start with a Clean SlateThe original stick-framed kitchen addition, built in the middle of the 20th century, was too small for a growing family and didn’t match the original house. The solution was to tear it down and build a larger one with appropriate architectural details. ![]() ![]() ![]() |
Adding to a Beautiful Old Home
This beautiful Connecticut farmhouse, which dates back to the 1780s, needed a new kitchen. Its existing 10-ft. by 12-ft. kitchen was added in the early 20th century and last remodeled in the 1980s. The cramped, dark space didn’t work for a modern family, and nothing about the addition matched the attractive exterior of the center-hall Colonial it was connected to.
So in partnership with a good design team, our clients hired us to replace the unfortunate addition with a larger one featuring a modern kitchen and a functional mudroom. The roughly 18-ft. by 18-ft. addition would require a new foundation and removal of the existing one.
Prep for the FoundationA few days before the foundation pour, the crew formed and placed a 12-in. by 24-in. reinforced-concrete footing in a few hours using a 3000-psi concrete mix. A keyway (series of grooves) cast into the top of the footing prevents the foundation walls from sliding from soil pressure. ![]()
|
The spacious lot had great access for equipment and concrete deliveries, but the kitchen addition would be on the uphill side of a slope with an amazing 100-year-old maple nearby. We would need to lower the grade so that the framing and sheathing would be sufficiently above grade to discourage decay and insects.
Unfortunately, the maple and an existing water line running from the well meant we couldn’t lower the grade more than a few inches and not much beyond the new foundation footprint. Of course, we could have maintained the existing grade and raised the addition above it, but that would have meant a step up into the kitchen addition from the main house and a trip hazard.
Foundation and Floor System
We wanted to keep the addition as low as possible, so we built the floor system inside the top of the crawlspace foundation. This method minimized site disturbance and allowed the new kitchen floor to line up with the floor in the main house without a step. It’s the same foundation and floor system we use to keep any new house or addition close to grade for greater accessibility or because of site conditions.
Place and Finish the FoundationThe concrete mixer was able to reach all of the foundation forms with a chute extension provided by the foundation contractor. It took 8 yd. of 3500-psi concrete to form the 3-ft.-tall, 10-in.-thick foundation walls.
|
With old houses like this one, the deepest courses of stone in a stone foundation are only minimally mortared, especially on the soil side. The stones become unstable when the soil around them is removed during excavation.
Even though a full basement is only a little more money in a situation like this, we opted for shorter crawlspace walls over a full-height basement to minimize excavation close to the existing stone foundation to prevent undermining it. We like crawlspaces under kitchen additions because they make future changes and upgrades easier compared to slab-on-grade or pier-and-beam foundations.
Place and Finish the SlabA gravel layer and 15-mil plastic sheeting under the crawlspace slab prevent water in the soil from moving through the slab into the crawlspace and evaporating, increasing humidity levels inside the house. The slab was poured and finished the same day as the foundation, using the same concrete delivery. ![]() ![]() ![]() |
Final Touches
With the foundation and floor system in place, the rest of the addition was very conventional: 2×6 walls with insulated sheathing and dense-pack insulation and a drywall interior. We framed the roof with trusses and had the HVAC contractor rough in the refrigeration lines over the kitchen ceiling for the kitchen and second-floor minisplits for cooling and supplemental heating. Once the drywall was hung and finished, we insulated above the ceiling with loose-fill cellulose.
Frame the FloorTwo mudsills connect the walls and floor system to the new crawlspace foundation walls. The wood elements are separated from the concrete with plastic seal sealer.
|
In addition to the new kitchen and mudroom, we did some other work on the house too. We rebuilt and replaced gutters and flashed the dormer windows with copper when we installed a new cedar roof. Our electrical contractor moved the electric lines underground when a new higher-amp service was installed. It was a satisfying project and it was nice working with kind, enthusiastic clients committed to preserving their beautiful old house. It’s rewarding to see how the new addition looks like it’s always been there.
Building as UsualOnce the floor system was finished, the rest of the kitchen addition was typical construction: 2×6 walls, a truss roof, and clapboards over taped water-resistant insulated sheathing. ![]()
|
— Dave Seegers is a partner with Hudson Valley Preservation in Kent, Conn. Photos by Patrick McCombe.
From Fine Homebuilding #329
RELATED STORIES
Fine Homebuilding Recommended Products
Fine Homebuilding receives a commission for items purchased through links on this site, including Amazon Associates and other affiliate advertising programs.
Not So Big House
A House Needs to Breathe...Or Does It?: An Introduction to Building Science
Homebody: A Guide to Creating Spaces You Never Want to Leave